Flow Wrap Packaging




Flow wrappers, or Horizontal Form / Fill / Seal or HFFS for short, is for when it makes sense to " push " a product vis-a-vis drop a product a la Vertical Form / Fill / Seal VFFS.
​
Film for flow wrap packaging is our strong suit. We have films for many products packaged on flow wrappers ( see applications ).
​
​
​
​
​
Images courtesy of Barrington Packaging Systems.
Flow wrappers are complex. They require constant care and feeding because they take a beating on a daily basis.
​
​
​
While there are a number of troubleshooting guides for horizontal flow wrappers, this one is in our opinion the best.
​
Flow wrappers require a stiff film ( high secant modulus ) , high slip ( low coefficient of friction ) , and film with differential melt temperatures. Either BOPP or lamination. A monololayer film will not work.
​
Flow wrapping and overwrapping are synonymous.
​
Seals are usually made with a heated roller to make the machine direction
( MD ) seal and bare metal jaws to make the end, or transverse direction ( TD ) seals.
For this reason, a " coex " BOPP prope, or film with thin layers of Low Density Polyethylene LDPE are a must- have to prevent film from sticking to the sealing surfaces.
​
Laminations of film with differential seal temperatures are easy to run on flow wrappers. This illustration is checks packaged in a lamination of polyester ( over 500 degrees melt temperature and LDPE sealing layer which has a melt point of around 300 degrees F.
​
​
​
​
​
​
​
​
Just like cars, there is range of new and used flow wrappers on the market ranging from entry level small flow wrappers to elaborate fully automated multi lane models.
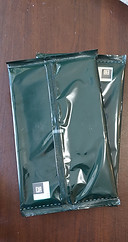

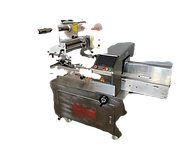
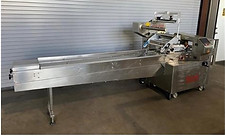


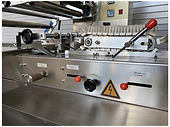
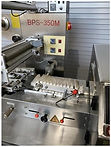
